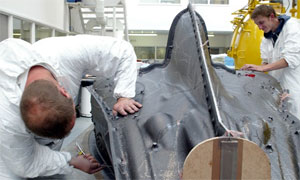
Das erste Monocoque des
Renault R24 nimmt Gestalt an: Das Kunstharz-Modell ist fertig. Der nächste Schritt erfordert nun noch höhere Präzision: die Abnahme der bereits aus Kohlefaser bestehenden Negativformen für die Produktion der tragenden Überlebenszelle.
Zuschneiden der Kohlefaserplatten
In diesem Stadium verfügen die Verbundstoff-Techniker über ein sehr akkurates Chassis-Modell, das dem endgültigen Teil bis auf eine Toleranz von 0,05mm entspricht. Es besteht aus hellblauem Epoxydharz und wurde in mehreren Arbeitsgängen von Computer-gesteuerten Werkzeugmaschinen bearbeitet. "Nachdem die endgültige Form herausgearbeitet ist, lackieren wir die Teile schwarz und polieren sie auf Hochglanz", erklärt Verbundstoffexperte Colin Watts. "Was nun folgt, ist um Einiges komplizierter, denn wir müssen entscheiden, auf welche Weise wir die Formen abnehmen: Bei besonders großen Teilen oder solchen mit sehr komplexen Oberflächen setzen wir die Produktionsform aus mehreren Abschnitten zusammen." Die beiden Hälften, in denen später das Monocoque geformt wird, bestehen zum Beispiel aus sechs verschiedenen Sektionen: vier für die obere Form und zwei für die untere.
Modellieren der Karbon-Zuschnitte
Wenn der Monocoque-Dummy bearbeitet, lackiert und mit einem Trennmittel zum leichteren Ablösen der Formen versehen ist, belegen die Renault F1-Techniker die gesamte Oberfläche mit Papier, das sinnvoll zugeschnitten wird und nun als Muster für die Teile der Form dient. Die Verbundstoff-Techniker verwenden diese Schablonen, um exakt identische Stücke Kohlefaser zuzuschneiden. Auf den ersten Blick wirkt der rohe Kohlefaser-Verbundstoff wie Lakritz – nicht nur weil er schwarz, sondern auch von ähnlicher Konsistenz ist. Die Wirklichkeit sieht natürlich anders aus: "Der von uns verwendete Karbontyp wird in großen Platten hergestellt", erklärt Colin. "Zum Einlagern werden sie auf –18°C tiefgekühlt. Bei Raumtemperatur ist das Material so weich, weil es viel Harz enthält. Dies stellt sicher, dass die Oberflächen der Formen später absolut eben sind." Die zugeschnittenen und „aufgetauten“ Karbon-Stücke werden nun vorsichtig auf dem Kunstharz-"Monocoque" aufgebracht.
Einsatz für den Autoklaven
Nachdem sich die Kohlefaser-Zuschnitte an ihrem Platz befinden, verschwindet der gesamte Aufbau in einem großen Plastiksack, aus dem daraufhin die Luft herausgepumpt wird. In diesem Zustand schieben die Techniker die Rohform in den „Autoklave“ genannten Ofen, wo sie unter hohem Druck von rund sieben bar „gebacken“ werden. Jede Seite der entstehenden Form ist mit einer Vielzahl von Gewindeschrauben und Muttern versehen, um sie in den folgenden Prozessschritten perfekt justieren zu können. "Nach dem Abkühlen nehmen wir die Formen vorsichtig von der Monocoque-Schablone ab. Das Kunstharz-Modell hat damit seine Schuldigkeit getan und wird entsorgt", fährt Colin fort. "Die neuen Negativformen weisen noch scharfe Außenkanten auf, die wir akribisch abschleifen. Jetzt können wir sie zum Bau der neuen Chassis verwenden. Die Formen kommen übrigens über die gesamte Saison hinweg zum Einsatz." Um noch flexibler auf neue Entwicklungen reagieren zu können, stellt Renault F1 zudem jeweils zwei Formensätze her: Damit ist die Fertigungsabteilung in Enstone in der Lage, mehrere Chassis parallel zu produzieren.